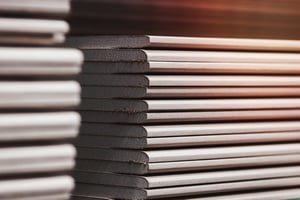
Staying Ahead of the Competition with Industrial IoT
Manufacturing - Americas
Business Overview
Business Focus
ManufacturingBased in the United States
125-year-old iconic American manufacturing company with 68 plants across the US.Business Case
Experiencing Docker scale issues. Docker was too complex for the team to use. The one Linux expert who was proficient at using the command line, was losing the productivity battle.Container Platforms
Docker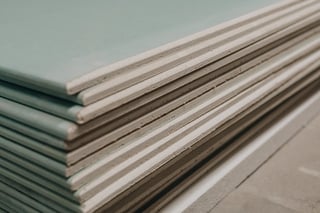
Customer Objectives
Company Background
This US manufacturer is the world’s largest producer of drywall panels, joint compound and related construction products that are used to construct walls, ceilings, roofs, and floors of residential, commercial, and institutional buildings, and various other industrial applications.
The company is also the largest ceiling suspension grid manufacturer in the world, the largest distributor of wallboard in the United States, and the world’s second largest ceiling tile manufacturer and in leading positions in cement board systems, and plaster wall systems.
They strive to differentiate the company from competitors through innovative products produced efficiently in 68 plants across the US.
The Challenge
This manufacturer was an early adopter of Docker containerization technology. It is also no stranger to innovative manufacturing techniques having deployed manufacturing sensors to feed the plants programmable logic controllers (PLCs) long before the industrial sector started talking about the Industrial Internet of Things (IIoT) or Industry 4 applications.
Even though they had a technology expert proficient at Docker containerization– they were experiencing Docker scale issues. Docker was so complex to use that even the one Linux expert who was proficient at using the command line Docker coding, was losing the productivity battle. He and the data science team were charted with the development and deployment of applications needed to keep high-speed manufacturing plants running by creating fail safe capabilities designed to isolate a plant failure to one small section taking it offline, while the rest of plant continues to operate. Scale issues arose because the applications are deployed many times per day, as he and the team would iterate computer code changes to keep the transformation project moving forward.
And the data scientists who supported this project were not at all proficient utilizing Docker and it’s complicated command line execution requirements, putting the project time line at risk.
The Solution
Both challenges were addressed using Portainer. The applications they are developing measures bubbles in millionths as a high-speed drywall board product races by on the manufacturing line. The output of the application predicts the physical strength, bond of the chord to the paper of the drywall board, and ensures each board meets exacting specifications.
Today, the application associated with this project, is deployed up to 40 times per day as infrastructure and data scientist experts iterate changes to eliminate all high-risk situations in the control system.
Prior to Portainer this work was all done with Docker command line code. As this manufacturer began to scale the application out to 21 plants the need for manual command line creation was limiting their ability to scale. The data scientist put it this way;
"The second [enterprise project we are deploying] is a real-time video feed of a drywall board on a high-speed production line. This application is in development so there are continuous updates. Up to 40 times a day we push and pull…a lot of action. Before Portainer this was all done manually with command line. Because of Portainer we can now deploy the same containers to all of the cameras in the plant all at the same time. Without Portainer we would have to add another “me” to basically just enter command line code all day. Now I just click a series of buttons to deploy the newest image and then restart, and that’s it.”
Everything is deployed to on-premises computers, and the cameras and sensors are air-gapped from the web to ensure total security. Portainer also helps keep applications secure because they use the build- in easily configured role-based access control (RBAC) capabilities.
The Results
“By using Portainer, and because after code is deployed we keep everything air-gapped we lower risk by decreasing the vulnerability attach surface”, says the Linux Server Team Leader.
This small team ensures that dozens of plants keep running. They prevent line stoppages by using newer algorithms delivered via Portainer to predict problems. And the application isolates problems so the line doesn’t stop and the product gets out the door. This team knows they contribute to the top-line by ensuring production yield aligns with the daily, weekly and monthly sales goals.
Given this organization was taken private a number of years ago, “top line contributions are not shared with vendors”, says the lead data scientist, “but we do our part to effect the top line by making sure product gets out the door.”
What does a line stoppage cost this large manufacturer?
"It’s difficult to quantify," says the team leader, "but it would be expensive. This project isolates at the conveyor level not the whole line. We designed this new system to accommodate little down times in small portions of the line without affecting the rest of the line. So we don’t have expensive full line stoppages.”
The average large US manufacturer loses $532,000 per hour in lost revenue, financial penalties, idle staff and restarting lines.
This project is on time and on budget partially due to Portainer. To get proficient with Docker
“...takes a lot, months, even quarters to get proficient with Docker. Some people never get there,” says the Linux leader. “Portainer makes the efficiency producing technology of containers available to all of us technicians and the data scientists.”
And the next problem they plan to tackle with the help of containers and Portainer –supply chain. Specifically, because of the disruption to global supply chains, finding reliable alternative product is critical to efficient plant operations. Knowing the demand side requirements is aided by new algorithms that this manufacturer is planning to containerize to speed time to benefit.
The Results
By extending the power of containerization to the entire team saving 12.5% of the teams time 1hr/day. Estimated savings approx $51,449.
Eliminated the need to hire an additional Linux expert saving $124,090/year.
High-speed manufacturing plants maintain operation by implementing a project that ensures fail-safes isolate any failures to a small section, allowing the rest to keep running. If Portainer reduces just 1 hr of downtime/yr in a single plant, the savings could amount to $532k/yr.
Cameras that can detect production problems that could cause a line stoppage before they occur.
Quotes from the Team
"We have had tons of sensors connected to programmable logic controllers (PLCs) for decades. We have essentially used Portainer to turn dumb cameras into a smart IoT device."
"Portainer lowers the barriers to entry for container for our entire group. There isn’t a lot of container expertise out there and we aren’t a high-tech company so you won’t find a lot of expertise in house. Portainer is a huge thing for us to scale, create repeatability and ease of use."
“Portainer makes the efficiency producing technology of containers available to all of us technicians and the data scientists.”
"If my CFO came to me and told me I couldn’t have Portainer, I would tell him. ‘I use the Portainer web hooks capability to repull and restart these containers. At the scale we are at, it would take 2 people, both getting bored using command line code all day long if I didn’t have Portainer."
"The best thing is Portainer is an “out of the box” solution. Easy to deploy – made for Docker."
"With Portainer we can update a plant with the push of a button. It's a continuous integration and deployment capability."